熔模铸造工艺流程
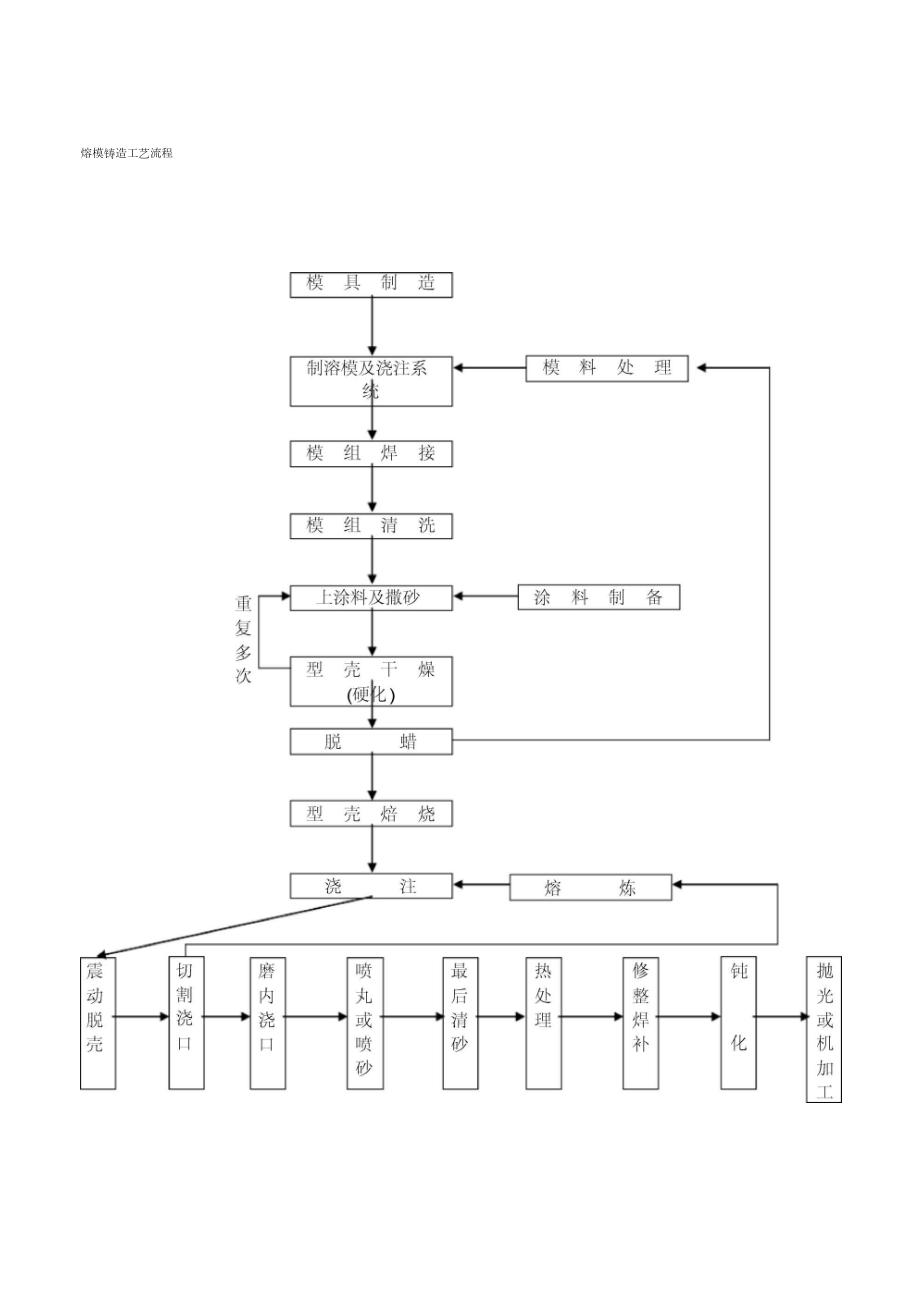


《熔模铸造工艺流程》由会员分享,可在线阅读,更多相关《熔模铸造工艺流程(28页珍藏版)》请在装配图网上搜索。
1、熔模铸造工艺流程制熔模用模料为日本牌号:K512模料模料主要性能:灰分铁含量熔点针入度0.025%灰分的10%98.6%即ZrO265%TiO20.25%Fe2O3w0.10%AI2O3w1.0%2、PH6.00.53、密度4.5g/cm34、外观灰白色或掺灰黄之白色5、锆粉使用300-325目6、锆砂使用80到100目(AFS80-95)制壳用煤矸石粉砂煤矸石粉砂是用高岭土经高温煅烧而成的熟料。煤矸石粉用于配制背层涂料,煤矸石砂是制背层型壳的撒砂。技术要求:1、化学成分AI2O3SiO2TiO2Fe2O3CaOMgOK2ONaO灼减2、岩相莫来石方英石非晶态3、密度4、砂粉尘量含水量10小时
2、。二、操作程序1、在沾浆机中加入90kg硅溶胶;2、开动沾浆机使其旋转;3、润湿剂以每公斤硅溶胶1.6CC的例加入,混均匀;4、然后将320kg锆粉,缓慢加入桶中,注意防止粉结块,靠搅拌将粉料搅开;5、按每公斤哇溶胶加1.2CC消泡剂的比例加入消泡剂,混匀。6、用4詹氏杯测涂料粘度,粘度应为32-38秒(气温低时38秒,气温高时32秒);7、如粘度过高,加硅溶胶调整;如粘度过低,加锆英粉调整。&涂料粘度调整好后,盖上浆桶,以免蒸发,继续搅拌12小时以上,即可使用;9、正常生产时,每班制壳下班前应按比例添加材料,直到涂料浆高度达工作标准,测定其粘度,粘度合格后,继续搅拌8小时以上可使用;注:二层
3、涂料除不加润湿剂和消泡剂外,其它操作均同面层,粘度调整好后继续搅拌10小时以上。三、操作注意事项1、涂料配制时要严格按操作程序加入硅溶胶、润湿剂、锆英粉、消泡剂,加料次序应正确。2、涂料浆务必保持干净,不得有蜡悄、砂粒等。3、涂料浆中不得有过多的气泡。4、涂料浆粘度每班上、下班前均需测定,调整。5、面层涂料浆如不使用,工作寿命不得超过14天。二层涂料浆如不使用,工作寿命不得超过30天。背层涂料配制一、工艺参数背层涂料粉液比(硅溶胶:煤矸石粉)1:1.4背层涂料粘度122.0秒全部新配背层涂料搅拌时间6小时,部分新配料搅拌时间4小时操作程序1、在沾浆机中加入170kg硅溶胶;2、开动沾浆机,使其
4、旋转;3、边搅拌边缓慢加入240kg煤矸石粉,注意防止粉结块,靠搅拌将粉料完全搅开;4、用4#詹氏杯测涂料粘度,粘度应为10-14秒之间;5、如粘度过高,加硅溶胶调整;如粘度过低,加煤矸石粉调整;6、涂料粘度调整好后,盖上浆桶,以免蒸发,继续搅拌6小时以上,即可使用;7、正常生产时,每班制壳下班前应按比例添材料,直到涂料浆高度达工作标准,测定其粘度。继续搅拌4小时以上可使用。操作注意事项1、检查涂料粘度前至少搅拌5分种;2、涂料浆粘度每班开始、中间和完毕时均需测定,粘度超过规定时,必须调整;3、背层涂料浆如不使用,工作寿命不得超过60天。工艺参数1、清洗后干燥静置45分钟以上的模组可进行制壳;
5、2、制壳参数注:硅溶胶予湿剂为25%的硅溶胶溶液操作程序1、检查从清洗处推来的模组:是否完整,是整否已清洗过,清洗干燥后是否静置45参数一层数一面层二层背层半层涂料种类面层涂料二层涂料背层涂料背层涂料撒砂80-100目锆吵30-60目煤矸石16-30煤矸石温度C)18-2220-2422-2622-26湿度(%)50-7050-8050-8050-80干燥时间(h)8121214硅溶胶预湿剂浸预湿剂分钟以上。2、检查涂料和设备是否正常,如不正常应加以调整A、检查各层涂料粘度是否合适,混制时间是否合适;B、淋砂机和浮砂桶工作是否正常;C、室温、湿度是否正常。3、从运送小车上取下模组,以30C左右
6、角度将模组缓慢地浸入涂料浆中旋转。注意模组钩、槽和尖角处包在涂料中的空气应减到最少。4、以稍快速度取出模组翻转,使多余涂料滴除,在模组上形成完整均匀涂层。用低压压缩空气吹破模组孔洞和尖内角的气泡。若不能获得均匀完整涂层需重新沾浆(重复3、4步骤)5、将上有均匀涂层的模组伸入淋砂机中翻转,让全部表面均匀覆上一层砂。6、取出模组吊挂在运送小车上,等整车挂满后,推到适当位置存放8小时使面层干燥。7、将面层已干燥的型壳推到背层制壳间,制二层型壳处。&取下模组检查型壳角、孔处是否完全干燥,如有皱纹等情况,应立即向领班反应。9、取下型壳以柔和风吹去多余砂粒。10、把型壳浸入硅溶胶预湿剂中,不超过2秒,取出
7、后滴约5秒钟。11、把不再滴的型壳以一角度(30E左右)缓慢浸入二层涂料浆中约3-4秒。12、以稍快速度取出型壳,转动,滴除多余涂料,形成均匀涂层。如孔洞等处有涂料闭塞和堆积可使用低压压缩空气吹一下。13、将型壳伸入浮砂桶内,敷砂。当浇口杯缘已有砂时,即可缓慢抽出型壳,振落多余的砂粒。目视,应无任何区域尚未被砂覆住。如有无砂覆盖处可用于敷砂。14、把型壳吊挂回小车上,整车挂满后,推到干燥区干燥12小时。15、一、二层干后,将小车推到第三层涂料处,取下型壳轻摇,去除型壳上松散的浮砂。16、小心反型壳浸入背层涂料桶中,轻轻转动最少10秒。17、取出型壳让涂料滴落,可挂在沾浆机上方;架上让涂料滴回浆
8、桶,拿下转动使各处涂层均匀。注意:防止浇口标缘处涂层太薄。18、将型壳伸入浮砂桶内,敷砂。当浇口杯缘已达砂中,缓慢抽出型壳,振落多余砂粒19、把型壳吊挂回小车上,整车挂满后推到干燥区干燥12小时。20、重复15-19步骤制第四、第五层。21、重复15-17步骤制半层,干燥时间最少14小时。操作要点1、严格控制壳间湿度、温度。2、每层型壳壳必须干燥后才能制下一层型壳。3、严格执行操作程序,认真仔细制壳。特别注意制好面层,确保孔和尖角处涂料与模组间无气泡,无涂料堆积、糊住孔等现象。4、制下一层前必须抖掉上一层的浮砂。5、工作手套必须保持无砂和无涂料,以免涂料受污染。应经常清除涂料表面的蜡悄等。6、
9、面层型壳刚制完不得置于风扇前后。注意面层和二层干燥速度不应过快,干燥时间不过长,以防出现龟裂等缺陷。7、取、挂型壳必须轻拿轻放,推送小车时要平稳,防止型壳碰撞,碰伤。&型壳破裂需修补后才能送往下一工序。修补时应清理掉损坏区域多优质产品的陶瓷材料,在处一层一层制壳,直至它和其它部分一样厚,注意修补的不得将整个型壳沾浆。一、工艺参数脱蜡最大压力脱蜡温度达到0.56Mpa压力时间脱蜡时间0.75Mpa170C10分钟操作程序1、型壳准备A、把已达到规定干燥时间的型壳小车推到型壳储存区,从小车架上取下型壳。B、拆下挂钩、盖板等,并将浇口杯缘多余陶瓷材料去除干净。2、设备准备A、脱蜡用蒸汽发生器蒸汽压力
10、应为I.OMpa,最低不得小于0.7Mpa。B、仔细检查蒸汽脱蜡过滤网是否需清理或更换,防止脱蜡过程中出现跑蜡等事故。C、开始脱蜡前,对脱蜡釜进行压力试验,并予热1-2次。3、将待脱蜡型壳装在小车上,运送到脱蜡工部。4、把型壳快速装在脱蜡蒸汽釜装载车上,送入脱蜡蒸汽釜,立即关好机门。5、打开蒸汽阀,14秒钟内压力必须过到0.56Mpa,温度达到160C。6、脱蜡时间至少10分钟。7、关闭蒸汽阀,打开排气阀,泄放蒸汽压,泄放应慢,在1分钟以上。8、压力表指示压力为零时,打开脱蜡釜机门,并打开泄蜡阀。9、反装型壳的装载车拉出,将型壳放在运输车上送到熔化车间。10、检查脱蜡后的型壳,将正常的型壳浇口
11、杯向下放在清洁的存放架上等待焙烧。有裂纹的型壳需修补。出现碎裂或成片剥落的,或裂纹超过0.5mm宽对铸件有影响的型壳应通过质检人员报废。11、型壳修补A、壳表面只有微细龟裂时,可在该处涂、沾涂料进行修补。B、型壳有孔和不影响铸件的大裂痕,可用一块干净壳放在有孔处再用耐火泥封上,干燥。操作要点1、脱蜡装卸型壳时务必小心,防止碰坏型壳。2、脱蜡时脱蜡釜机门必须关严,以免热量逸散。不要碰坏或刮伤炉门的密封填料,如有伤痕应即予以更换。3、装载循环动作愈快愈好,若延迟时间会造成型壳先期受热。因蜡料比型壳热膨胀大,易造成型壳损坏。4、适时清理蒸发桶管道,防止阻塞。输蜡管道要随时检查,确保管道在70-85C
12、之间畅通。每天用完后需用蒸汽清洗输蜡管。5、操作时要载好手套。开脱蜡釜机门时,绝不能将脚放在门下,防止流出的热水烫伤人。脱蜡用蒸汽发生器蒸汽输出量额定压力用水水质特性要求总硬度含油量碱度500kg/hI.OMpav0.03mgN/lv2mg/t12-18Cl-v300mg/l每天排污一次,每年除垢一次水质每天化验二次型壳焙烧900-1100C25分钟最多60分钟一、工艺参数焙烧温度焙烧时间最少操作程序1、仔细检查需焙烧的型壳,型壳应完好无缺陷,有缺陷的型壳必须修补好。2、检查焙烧炉炉床是否平整干净。3、用手套将型壳浇口杯边缘抹一下,防止砂子等进入型壳中。4、小心地把型壳装入焙烧炉中:(1) 后
13、浇注的放在炉后部,先浇注的放在炉前部。即后浇注的型壳先装,先浇注的型壳后装。(2) 型壳浇口向下放置在焙烧炉炉床上,型壳不要相互接触,不要滑动。(3) 型壳不要与炉壁按触,不要装到火焰喷到处,并离炉门要10公分。5、关上炉门。6、点火升温。炉内温度在900-1100C之间,型壳焙烧时间最少25分钟,最多不超过60分钟,焙烧好的型壳应为白色或蔷薇色。7、打开炉门,用叉子取出型壳,目视有无裂纹,同时翻转,将型壳浇口向上准备浇注。操作要点1、严格控制焙烧温度和时间。如温度过高,时间过长型壳会烧过,导致型壳强度降低和变形。如温度过低、时间过短型壳烧不透,其透气性差。2、焙烧炉各处温度应均匀。型壳放置应
14、合理,火焰不得直接喷到型壳上。3、防上型壳中掉人污物,装炉时型壳浇口应向下放置时,要用石棉布盖住浇口。4、开关炉门动作要快,防止炉温下降过多。5、炉床至少每周用扫把或压缩空气清理一次,确保清洁。熔炼金属使用快速炼炉,使用前应修好炉衬,常称筑炉。一、炉体构造快速熔炼炉正常使用时,炉体构造见下图。图中:1装料口,2出钢槽,3炉衬,4炉底,5石棉板,6石棉布,7为铜管感应圈。筑炉是完成感应圈7中间的1-6部分。二、筑炉程序1、筑炉材料准备(1)炉衬耐火泥准备,用70-80%耐火粘土加20-30%水玻璃,搅拌成膏状待用。(2)石棉板、石棉布或云母片若干。(3)炉衬材料,用40-45%MgO粉加55-6
15、0%MgO砂混合做炉衬材料。因它们的粒度分布对炉体的寿命影响极大,建议粉砂粒度分布如下:砂6目8目10目14目20目28目35目%1532.733.813.54.40.40.2粉100目150目200目270目325目以下%7.77.16.59.29.660.32、筑炉准备(1)铜管线之间隙,应糊上耐火泥。(2)炉底铺2-3层石棉板,厚度约6-10mm3、筑炉底(1)底部炉圈内侧衬以石棉布或云母片。(2)炉底石棉板上,一次铺以70-80mm高的炉衬材料,用撞棒捣实成为均匀致密,厚度约60-70mm的一层。(3)用叉状棒将其表面弄粗糙,再铺上70-80mm的炉料材料,用撞撞棒捣实。(4)重复(3
16、)直至捣紧面超过最低铜管圈20-30mm。(5)用圆形筑炉棒滚压使表面紧实,其后用耐火砖抹平,注意水平面及至炉顶的高度,将多余的筑炉材料削去(20-30mm厚)。(6)用水平仪测水平,在确定到炉顶的尺寸后,再次用圆形棒滚压表面。4、筑侧壁100kg熔炼炉侧壁壁厚指标:上部60mm下部75mm方法一(干式筑炉)(1)将烧结用型筒外侧,用砂纸擦干净,铁锈要全部去除。(2)将清洁型筒置于炉子感应圈内,注意必须与感应圈同心,必要时用测量工具测定以调整型筒位置,保证同心。(3)型筒定位后,用钢料压稳并用木盖盖住。(4)使用叉状棒将石棉布或云母片与型筒之间的底部炉衬材料推弄粗糙。(5)在型筒与炉圈的环状圈
17、内,一杯杯装入炉料,每次装料高度约20-40mm,用捣棒沿圆围顺序捣实。(6)重复(4)、(5)之动作逐层捣实,直至离炉顶50mm为止。(7)顶端和装料口、出钢槽用同样的炉衬材料另添加5-10%的水玻璃制作。方法二(湿式筑炉):在型筒外侧卷上厚纸板,置于炉子感应圈内,注意与圈同心。定位后用钢料压稳,后来步骤同方法一。修好炉衬后,通电将纸烧掉,拔出型筒。为避免炉底破裂,将炉底弄成大圆弧。并在炉壁涂上50%水玻璃溶液以防炉体崩溃,且可促进烧结。放入炭块,干燥2-3小时。或将石墨电极放到炉衬内通电发热,进行干燥。5、烧结(1)在炉膛内装好金属料。干式筑炉一般加熔点较低的生铁;湿式筑炉第一次装料,不要
18、大粗或太细。防止太粗重,搬运不便碰坏炉壁,太细的造成搭桥,使炉壁严重侵蚀。(2)送电,缓慢升温,在700-800E时保温适当时间,让筑炉材料中结晶水完全消失,然后升温到1450C左右。(3)增加电力,使最初装的料熔化,再继续投入小块,一次添加5kg左右,注意勿加入生锈和含砂材料,当金属液升到距炉顶50mm处,干式筑炉需倾动炉体,将熔断的型筒去除。(4) 再升高电力,使金属液温度达1700C左右,降低电力保温,约1小时,完成烧结。(5) 关掉电,让金属液冷至1560-1570C,除渣、脱氧、浇成分样块,再次除渣,把金属液浇到铸锭模中。(6)完成烧结后可加料继续开炉。也可停炉,用原2/3冷却水使炉
19、衬冷却3-4小时。6、炉衬的检查与修补生产中炉衬应不断检查和修补。不连续操作时,冷炉开炉前,应详细观察炉顶,壁、底是否要修补,在连续熔化时,每出钢一次,应从炉顶观察到炉底是否需要修补。炉衬修补分大修和小修。大修是重新筑炉,两次大修门熔化钢水次数称炉衬寿命或炉龄,一般为80-150次。小修是每天都要进行。(1)出水口和装料口修补。出水口和装料口易破损,开始作业前都需修补。在边续作业中,也有边熔炼边修补的。修补是以其相同的耐火材料填补。(2)壁面龟裂。裂痕在2mm以下的不必修补,超过2mm的裂痕需修补;先除掉四周炉渣;将盛有修炉材料的纸顶在裂痕下端;使用U型铁针,将材料挤入裂口;用混有水玻璃的筑炉
20、材料将表面压挤抹平。(3)壁面破损或小范围侵蚀先去除四周炉渣;涂上水玻璃;以混有水玻璃的筑炉材料压挤抹平;表面再涂上水玻璃。操作要点1、严格按照操作程序筑炉。2、炉壁厚度要按规定,炉壁太厚则炉容量变小,效率差;但炉壁过薄,如偶有破裂,钢液触及感应圈将引起爆炸事故。3、筑炉材料不能混入砂土、铁屑、木草屑和其它杂物。4、筑100kg炉体约需一日,当装料口、出钢槽完全干燥后才能使用。5、刚筑好的炉衬必须先烧结。一般是让金属液保持在修补处以下100mm,经过适当时间保温后才让金属液上升,恢复正常作业。炉料和配料炉料1、新来的钢料必须经检查化学成分,化验合格才可使用;2、炉料高清洁干净无杂物;3、不同材
21、质钢料应分开堆放。配料计算1、根据合金牌号、技术要求,确定其控制成分,然后计算炉料中各无素的含量(包括烧损量),按下式计算:K=Ko/l-S式中:K-炉料中某元素的含量(%)Ko-钢液中某元素的控制含量(%)S-某元素的烧损率(%)附:快速熔炼元素烧损率(%)=1=元糸CSiMnCrTiAlWVMONi碱性炉5-1030-4020-305-1040-6030-503-5-505-2002、根据炉料总重量,计算出各元素应有的含量;3、计算出回炉料中各元素的重量;4、计算出新料中各元素的重量;5、将炉料总重量中各元素的重量减新、旧料中各元素的重量即为各元素的不足量,不足的元素可用铁合金补充;6、将
22、计算结果相加,并核对是否符合配料成分要求。配料实例见下表。炉料和配料快速熔炼炉CF-8M(316)不锈钢配料计算单配料用原材料配比结果成分种类CSiMnNiCrMo%CSiMnNiCrMoCF-8M回收料0.0781.21.59.218.22.3400.0310.480.63.687.280.92废3040.881.01.78.218053.50.0430.540.914.3879.63纯镍991.00.99钼铁0.10.9862.82.160.0020.0211.356低碳铬铁0.090.60.9567.82.50.00180.0120.0191.695低碳锰铁0.11.0800.240.0
23、0020.0020.192硅铁0.2700.60.00120.421000.07921.4751.7719.05718.6052.276烧损率%51530030烧损量0.0040.220.5200.5580结果0.0751.251.29.05718.0472.276目标0.081.51.59-1218-212-3各国不锈钢牌号及化学成分美国铸造不锈钢化学(1)成分()和组织不造铸变rCOMsnMpsc他其牌钢锈形金的卜态状用号钢织组相牌号14-2a8002-511o0o030-物1oo44o424464004-511o0o050-物ooo44o-275111o0o0o0UC55.25oo444
24、UU1-O8-o251o0o0o0Ooo4433-FC04312-71-O8-o251o0o0o0LOoo4438-FC04312-811-O8-o251o0o0o0Ooo448023体氏奥12-811-O8-o251o0o020Ooo44o6312-713-O93a25151o0o0o0LOOoo4436312-8121-O93a25151o0o0o0Oooo44812-8121-O93a2o251o0o010素体或奥氏体0000442CF-8C347奥氏体中有铁18-219.0-12.2.01.50.00.00.0Cb8x素体000448C-10CF-16F303奥氏体18-219.0-1
25、2.1.502.01.50.10.00.1Sc0.20-0.00074635CG-8M317奥氏体中有铁18-219.0-13.3.-4.01.51.50.00.00.0素体000448CH-20309奥氏体22-2612.0-12.01.50.00.00.25.000440CK-20310奥氏体23-2719.0-21.71.50.00.00.22.050440CN-7M320奥氏体19-2227.5-32.0-3.1.51.50.00.00.0Cu3.0-4.0.50004470(1)除给出范围者外,均为最大值。各国不锈钢牌号及化学成分日本铸造不锈钢化学成分(%)牌号CSiMnPSNiCr
26、MoCu其他SCS115.00-7.0023.00-27.001.50-2.500.101.501.000.040.04SCS128.00-11.0018.0-21.000.202.002.000.040.04SCS138.00-11.0018.00-21.000.082.002.000.040.04SCS13A8.00-11.0018.00-21.000.082.001.500.040.04SCS1410.00-14.0017.00-20.002.00-3.000.082.002.000.040.04SCS14A9.00-12.0018.00-21.002.00-3.000.081.501.
27、500.040.04SCS1510.00-14.0017.00-20.001.75-2.751.00-2.500.082.002.000.040.04SCS1612.00-16.0017.00-20.002.00-3.000.031.502.000.040.04SCS16A9.00-13.0017.00-21.002.00-3.000.031.501.500.040.04SCS1712.00-15.0022.00-26.000.202.002.000.040.04SCS1819.00-22.0023.00-27.000.202.002.000.040.04SCS198.00-12.0017.0
28、0-21.000.032.002.000.04I0.04SCS19A8.00-12.0017.00-21.000.032.001.500.040.04SCS2012.00-16.0017.00-20.01.75-2.751.00-2.500.032.002.000.040.04SCS219.00-12.0018.00-21.00Nb+Ta10X0.082.002.000.040.04C%10X0.082.002.000.040.04C%8XC%G-X5CrNiMoNb18101.45810.061.51.50.0450.03018.0-20.02.0-2.510.5-12.5%Nb8XC%G-
29、X6CrNiMo18101.44080.071.51.50.0450.03018.0-20.02.0-3.010.0-12.0G-X3CrNiMoN171351.44390.041.51.50.0450.03016.5-18.54.0-4.512.5-14.5N0.12-0.22%各国不锈钢牌号及化学成分德国铸造不锈钢化学成分(%) 除给出范围者外,其它均最大值Mo量可由双方商定。 在难于确定条件下,如用于硝酸介质时,该钢种的允许最高含 两分钽可取代一分铌。我国铸造锈钢的牌号及化学成分(GB2100-80)0.040%,硅(见下图)注:1、需要作拼焊件的铬镍奥氏体不锈耐酸铸钢件中磷的质量分数应小于等于的质量分数应小于等于1.2%。2、图样和技术文件中不得采用代号。
- 温馨提示:
1: 本站所有资源如无特殊说明,都需要本地电脑安装OFFICE2007和PDF阅读器。图纸软件为CAD,CAXA,PROE,UG,SolidWorks等.压缩文件请下载最新的WinRAR软件解压。
2: 本站的文档不包含任何第三方提供的附件图纸等,如果需要附件,请联系上传者。文件的所有权益归上传用户所有。
3.本站RAR压缩包中若带图纸,网页内容里面会有图纸预览,若没有图纸预览就没有图纸。
4. 未经权益所有人同意不得将文件中的内容挪作商业或盈利用途。
5. 装配图网仅提供信息存储空间,仅对用户上传内容的表现方式做保护处理,对用户上传分享的文档内容本身不做任何修改或编辑,并不能对任何下载内容负责。
6. 下载文件中如有侵权或不适当内容,请与我们联系,我们立即纠正。
7. 本站不保证下载资源的准确性、安全性和完整性, 同时也不承担用户因使用这些下载资源对自己和他人造成任何形式的伤害或损失。